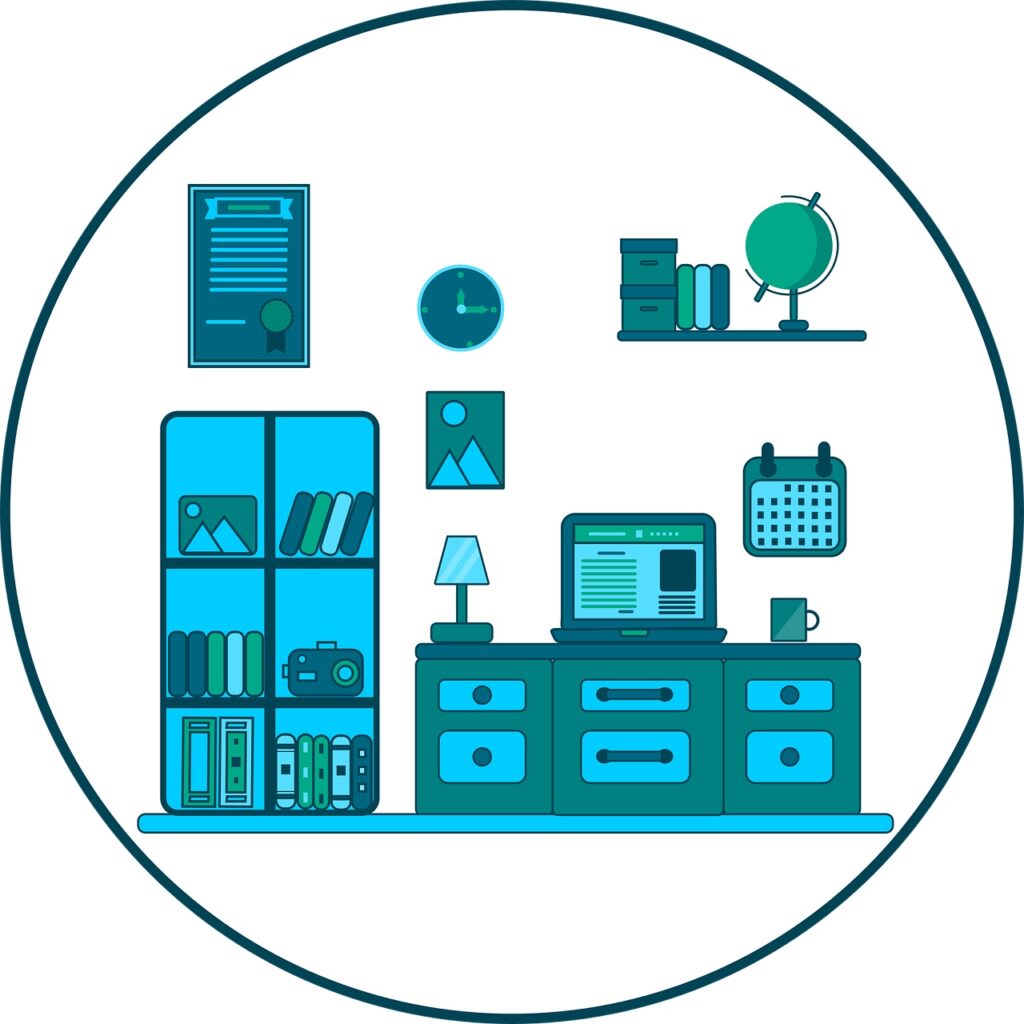
現代の製造業は、デジタル技術の急速な進化によって大きな変革を遂げています。
その中でも特に注目されているのが生産設備におけるIOT(モノのインターネット)の導入です。
IOTは、センサーや通信技術を活用して機器や設備を接続し、リアルタイムでデータを収集・分析し、生産プロセスを最適化する革新的なアプローチです。
従来の生産設備では、機械の稼働状況や生産データの把握に時間がかかり、人的ミスや生産効率の低下といった課題がありました。しかし、IOTの導入により、生産設備の遠隔監視や自動制御が可能になりました。
生産設備の稼働状況や異常検知、生産データの可視化などが効率的に行えるようになり、製造業における生産性向上や品質管理の向上が期待されています。
この記事では、生産設備におけるIOTの重要性やメリット、具体的な導入事例について探求していきます。生産性と効率性の向上を目指す製造業にとって、IOTは未来の成功につながる鍵となるでしょう。
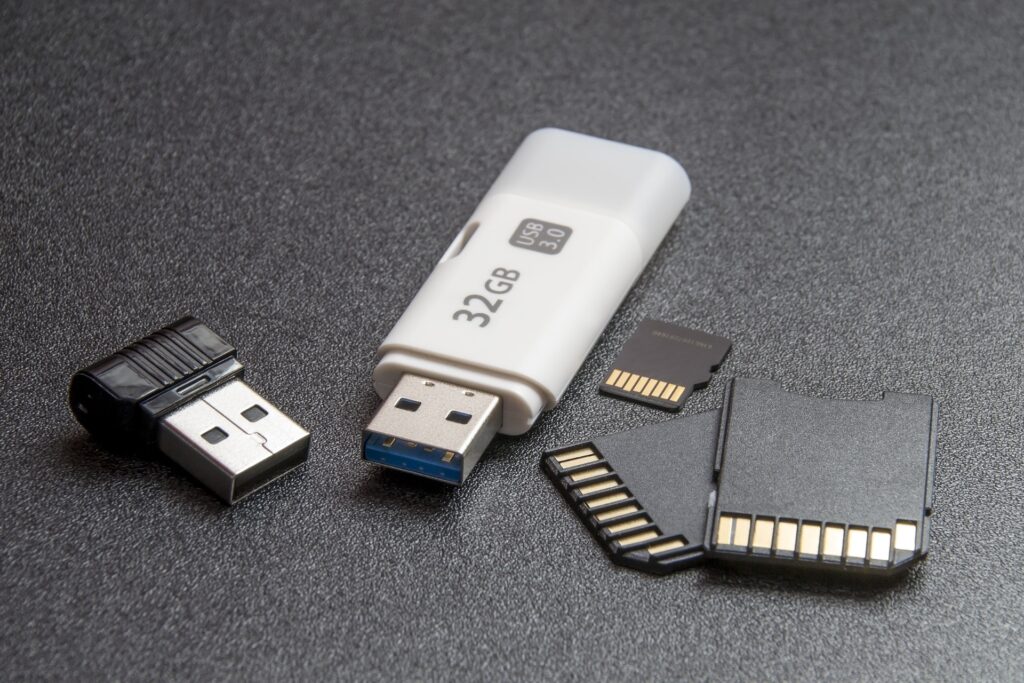
生産設備におけるIOTのメリット
- リアルタイムなデータ収集と可視化
- 異常検知と予防メンテナンス
- 生産データの活用と改善サイクルの加速
リアルタイムなデータ収集と可視化
IOTを生産設備に組み込むことで稼働状況をリアルタイムで可視化出来る様になります。いわゆる見える化というもので、生産ラインの効率化などに効果的です。
異常検知と予防メンテナンス
筆者の本業として、生産設備の保全業務を行っているのですが、異常検知と予防メンテナンスにおいでIOTを導入している装置としていない装置では保全業務のやりやすさが段違いです。
保全業務では異常の早期発見が重要で、異常に気づかない場合、不良製品が大量生産される可能性すらあります。
センサーの出力を監視し、故障となる兆候を取られた時点でアラームとして発報し装置を止めることでこれを防ぎ、品質リスクを最低限に抑えることが出来ます。
生産データの活用と改善サイクルの加速
何かを改善する時、改善前のデータと改善後のデータ収集は楽であればあるほど良いですよね。
IOTを導入している場合、生産データ自体は常に保存されています。問題点の分析やデータ収集にはそこまで手がかかりません。
加えて改善後のデータとの比較も容易に済む為、改善サイクルを加速することが出来ます。
IOTの具体的な導入事例
筆者の思う最も簡単なIOTの活用事例はPLC(プログラマブルコントローラー)、シーケンサーの活用です。センサーからの出力をPLCで取り込みデータ収集を助けてくれます。
異常を確認すると業務メールを送信したり、異常が発生した時点の前後10分間のデータを蓄積するなど使い方、可能性も多肢にわたります。
現在は各社から拡張ユニットも多種販売されており様々なニーズに答えてくれます。
自社でIOTに取り組む場合の簡単な事例はPLCといいましたが、現在ではメーカー独自の監視ソフトを自社開発されており、例えば真空ポンプなどを使用する生産設備では、日常点検・定期オーバーホールなど少し古いポンプでは目視で行うことが多く大変な手間が掛かっていましたが、IOT化が進むにつれて改善され、事務所からポンプデータを監視したり稼働状況を確認出来るのが一般的になっていっています。
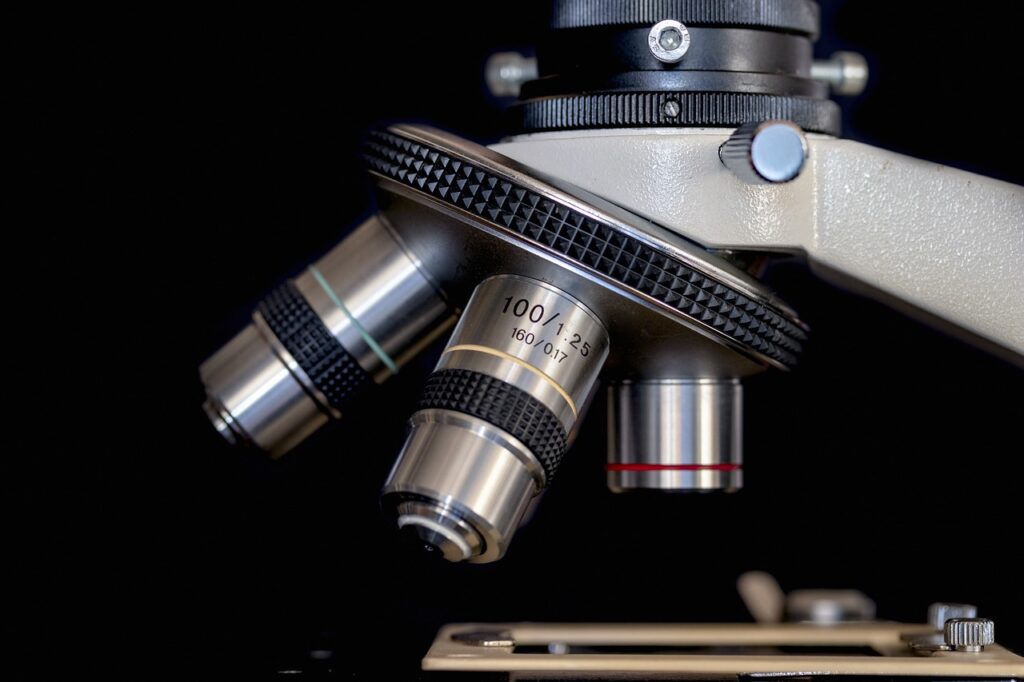
まとめ
IOTの導入には課題やリスクもあります。まず、センサーや機器の更新に費用が掛かる為、IOTに理解のない経営陣、管理職は導入を躊躇います。
また、センサーや機器が通信機能を持っていることからセキュリティ面でも十分な検討が必要です。
しかし、生産設備におけるIOTの重要性は今後ますます高まることが予想されます。市場の変化に対応し、生産性と品質を向上させる為にIOTの先駆者となり、より効率的で持続可能な製造業を目指しましょう。